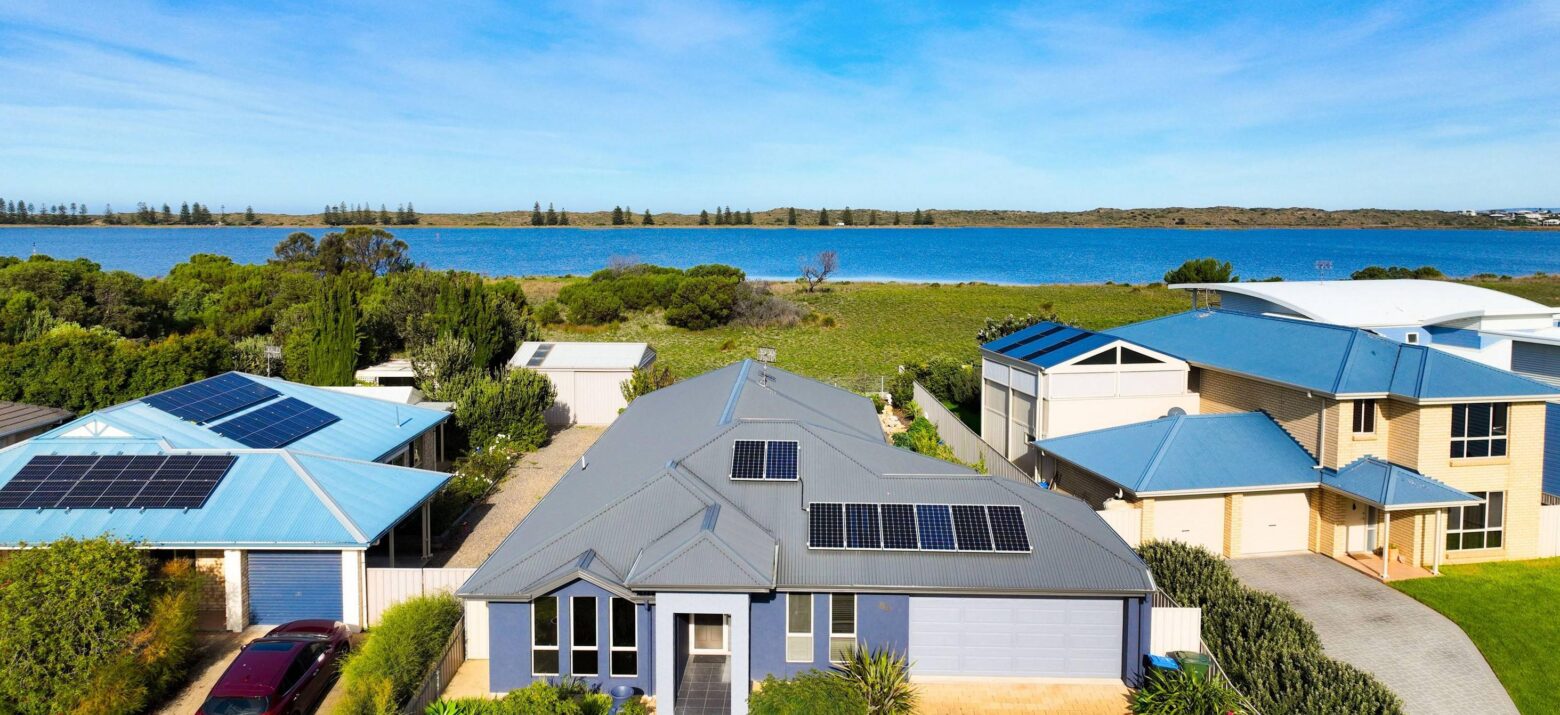
Industrial painting is a specialty field that requires specialized products. Choosing the right paint can make all the difference when it comes to protecting your equipment and creating a brand identity that sets you apart from competitors.
Industrial painters focus on practicality, not aesthetics. This is why they choose their products carefully.
1. Fast-drying
When you’re coating industrial facilities, the main goal isn’t to make it look pretty; it’s to provide protection for surfaces that will be subjected to harsh conditions. The right high-performance coating will resist corrosive materials, heat, chemicals, humidity, and other environmental factors that would otherwise wreak havoc on the structure. For this reason, many industrial paints feature a fast-drying formula that can be applied in a short period of time to prevent downtime at production facilities.
These types of coatings typically use a combination of polymers, resins, and fillers to form a dense film that provides a range of different aesthetic Painting Services, physical, and chemical characteristics compared with traditional air-drying paints. These include a wide variety of colors, textures, and finishes, as well as improved resistance to corrosion, abrasion, and extreme temperatures.
In addition to the aforementioned qualities, some industrial coatings also feature an intumescent fireproofing layer that can protect facilities and equipment from fires by expanding in response to excessive heat. The fireproofing layer is a critical component that can save lives and property, so choosing the right industrial coating is imperative to ensure proper safety and functionality for your facility.
2. Durable
Industrial painting projects require more than just a good finish and resistance to the occasional scuff. They must be durable enough to protect the painted surface from the wear and tear of daily use or the impact of physical or chemical aggression. This is why it is important to hire experienced professionals for your industrial paint and coating job.
A large part of a paint’s durability depends on the quality of its binder. Binders are responsible for binding pigments and creating the final, tough coating. They can be oil-based or latex-based, and the ratio of pigment to binder or PVC (pigment volume concentration) affects the thickness and sheen of the finished coat. The addition of extender pigments like silicates and zinc oxide can also help increase a paint’s durability.
Another consideration is its abrasion and corrosion resistance. This is determined by testing the paint against specific abrasion and corrosion-causing materials. Tests include exposure to salt fog, impact from abrasive or sand-blasted surfaces and accelerated weathering in extreme temperatures.
Some industrial paints may be designed as a primer or a topcoat, allowing you to get more done in one application. Moisture-cured urethane coatings are often used as a topcoat, as they handle higher dry service temperatures than epoxies and offer excellent abrasion resistance while maintaining color retention. Likewise, polyester polyurethanes can act as both a primer and a topcoat for long-term steel surface protection.
3. Intumescent fireproofing
One of the primary functions of industrial paint is to protect the surface it coats. It can withstand harsh chemicals and extreme temperatures, making it an essential component of many manufacturing facilities, warehouses, and other commercial buildings. In addition to stopping leaks and halting corrosion, some industrial coatings also offer fire protection. These fire-resistant products can help save lives and reduce damage after a fire in a facility, so they’re a must for any commercial design project.
These types of industrial coatings react to high temperatures by expanding and lowering their density. This helps them form an insulating layer that stops fires from spreading to other areas of the building. They’re often sprayed in multiple layers to achieve the desired effect. There are two types of fireproofing industrial paints, soft char and hard char. Soft char products release water that slows fires, while hard char products melt into sodium silicates and graphite to prevent them from burning.
Intumescent fireproofing industrial paint is not as easy to apply as regular paint, and it requires a lot of specialized knowledge. The best facility managers work with a professional coatings contractor to ensure the job is done correctly and that their facilities are in compliance with fire safety standards.
4. Environmentally friendly
Paint contains three main ingredients: pigments give the paint color; binder or resin helps it stick to surfaces and stay in liquid form; and solvents keep it from drying too quickly. While paints today are less toxic than in the past, many still contain what is known as Volatile Organic Compounds (VOCs) that evaporate into the air. These VOCs can cause a variety of health issues, such as headaches, dizziness, visual and respiratory impairment and even memory loss.
To help combat these health issues, Kaloutas offers a wide range of low-VOC industrial paint options for our clients. These environmentally friendly paints are formulated to reduce VOCs, while still providing excellent adhesion and performance. While conventional paint may cost more, it’s important to consider how much your health is worth.
Additionally, while conventional paint may contain a number of different chemicals, eco-friendly paint is free of any petrochemical ingredients. In fact, it is also biodegradable, which helps prevent environmental contamination. It is a good choice for anyone who wants to avoid harmful VOCs and is especially beneficial for those who are pregnant, have asthma or any other respiratory problems. Some of these paints are even made with natural materials such as milk proteins, citrus, clay or balsam. This makes them ideal for families with young children and pets.